Understanding Concrete Cracks: Causes and Solutions
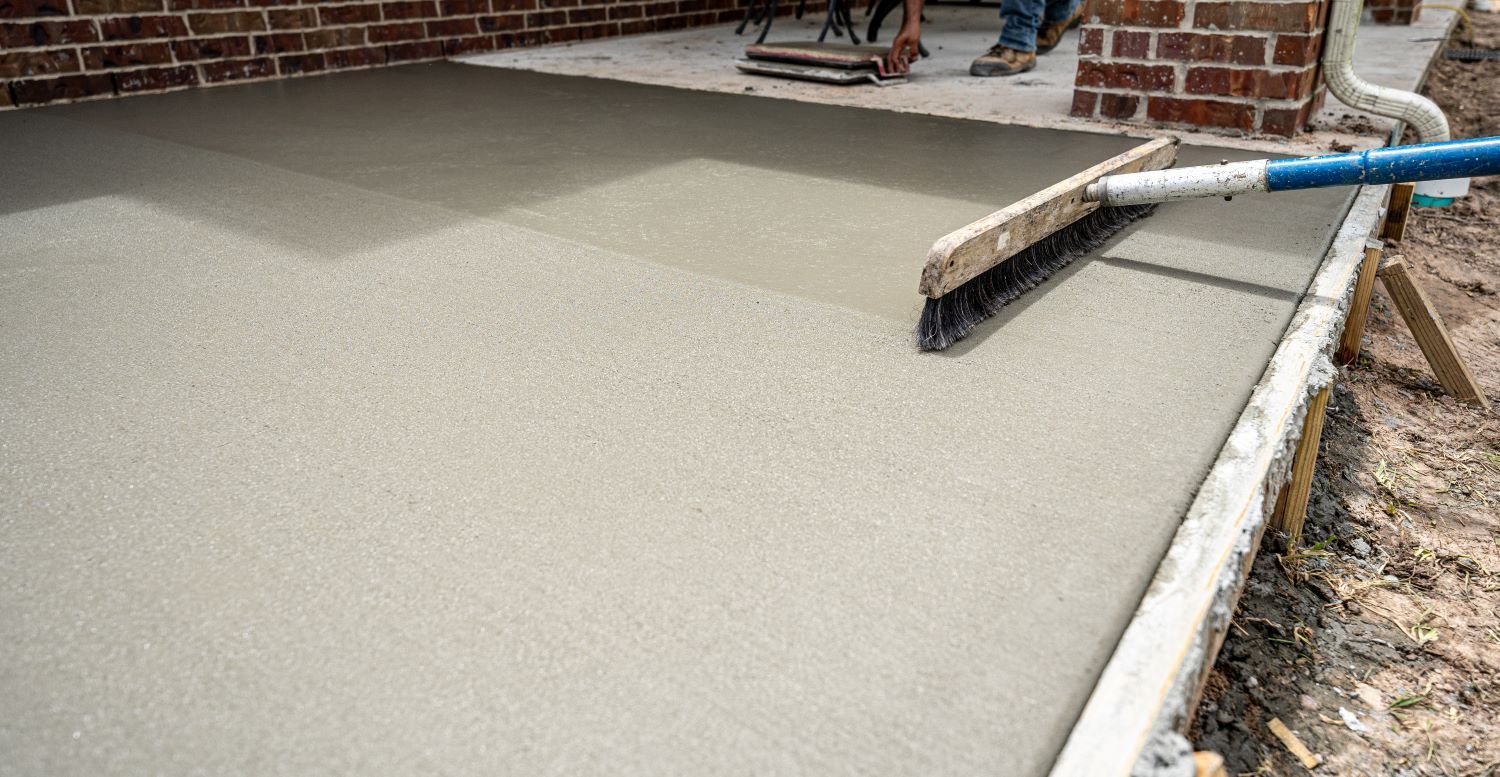
Concrete is a durable and versatile building material used in various construction projects, including driveways, sidewalks, patios, and foundations. However, despite its strength, concrete is not immune to cracking. Cracks in concrete can occur due to various factors, ranging from natural shrinkage to external forces and environmental conditions. In this article, we'll explore some common causes of concrete cracks and discuss how to effectively repair them.
1. Natural Shrinkage:
One of the most common causes of concrete cracks is natural shrinkage. As concrete cures and dries, it undergoes a process called hydration, where water reacts with cement to form a solid mass. During this process, the concrete can shrink slightly, leading to the development of hairline cracks known as shrinkage cracks.
Solution: Shrinkage cracks are typically minor and do not affect the structural integrity of the concrete. They can often be left untreated or filled with a concrete patching compound to prevent moisture infiltration.
2. Settlement:
Another common cause of concrete cracks is settlement, which occurs when the soil beneath the concrete compresses or shifts, causing the concrete to sink or settle unevenly. This can result in cracks, especially in areas with poorly compacted or unstable soil.
Solution: To repair cracks caused by settlement, it's essential to address the underlying soil issues first. This may involve stabilizing the soil with compaction or adding support beneath the concrete through methods like mudjacking or slabjacking. Once the soil issues are addressed, the cracks can be filled with a concrete patching compound or epoxy injection to restore the surface.
3. Freeze-Thaw Cycles:
In colder climates like St. John's Newfoundland, freeze-thaw cycles can wreak havoc on concrete surfaces. When water penetrates the concrete and freezes, it expands, putting pressure on the surrounding material and causing cracks to form. Over time, repeated freeze-thaw cycles can exacerbate existing cracks and lead to further deterioration.
Solution: Preventing moisture infiltration is key to preventing freeze-thaw damage. Sealing the concrete surface with a waterproofing sealer can help prevent water penetration and reduce the risk of cracking. Additionally, repairing existing cracks promptly and maintaining proper drainage around the concrete can help mitigate the effects of freeze-thaw cycles.
4. Overloading and Impact:
Heavy loads, such as vehicles or heavy equipment, can exert excessive pressure on concrete surfaces, leading to cracks or structural damage. Similarly, impact from dropped objects or construction activities can cause localized damage and cracking.
Solution: To prevent cracks caused by overloading or impact, it's essential to ensure that concrete surfaces are designed and constructed to withstand anticipated loads. Additionally, implementing protective measures, such as installing bollards or protective barriers, can help minimize the risk of damage from impact.
Conclusion:
While concrete cracks are inevitable, understanding the underlying causes and implementing appropriate repair solutions can help prolong the lifespan of concrete surfaces and prevent further damage. Whether dealing with minor shrinkage cracks or more severe settlement issues, consulting with a professional concrete contractor like Concrete Contractors St. Johns is crucial for accurate diagnosis and effective repair. With their expertise and specialized repair techniques, they can help restore your concrete surfaces to their optimal condition, ensuring long-lasting durability and performance.
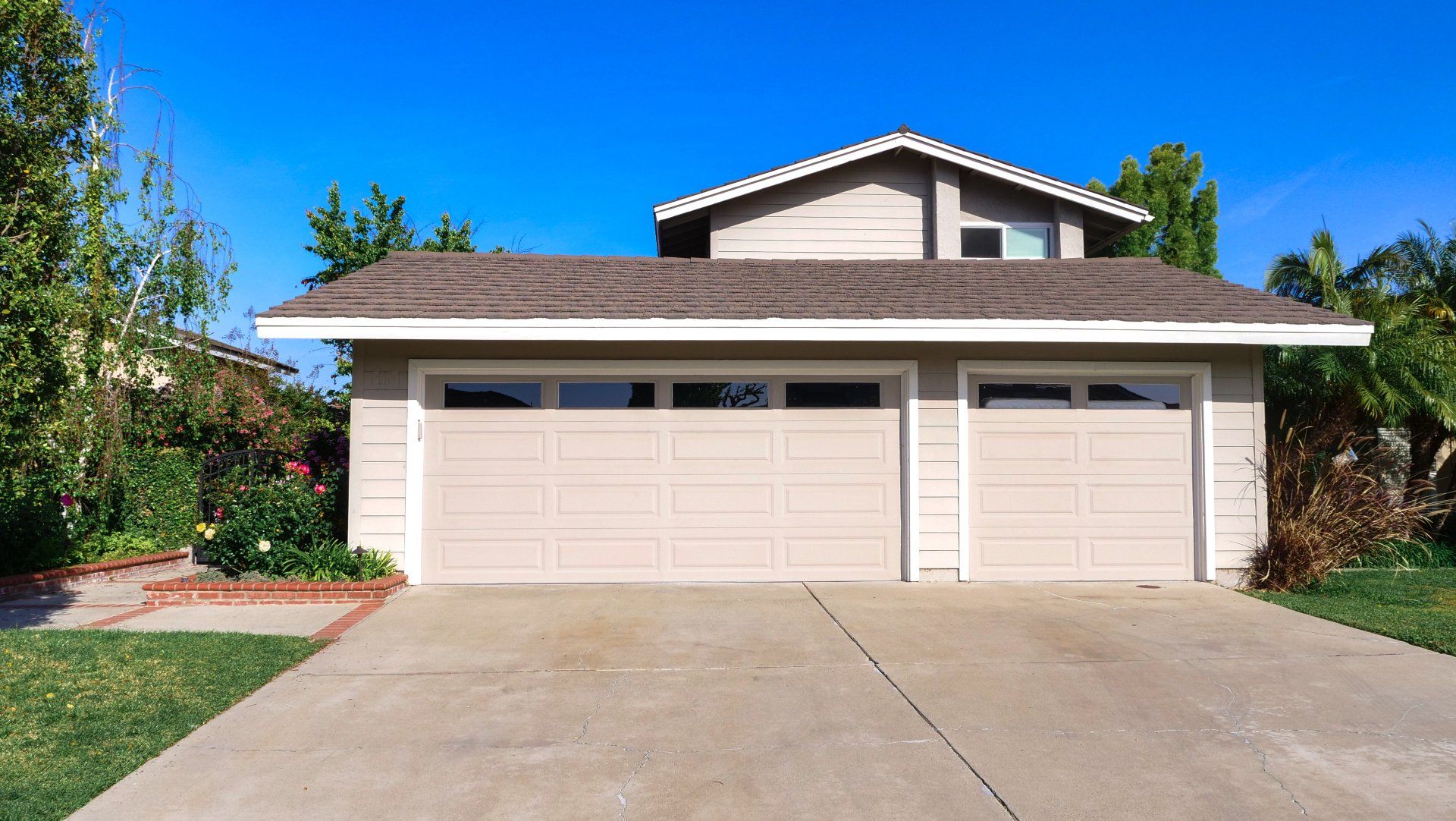
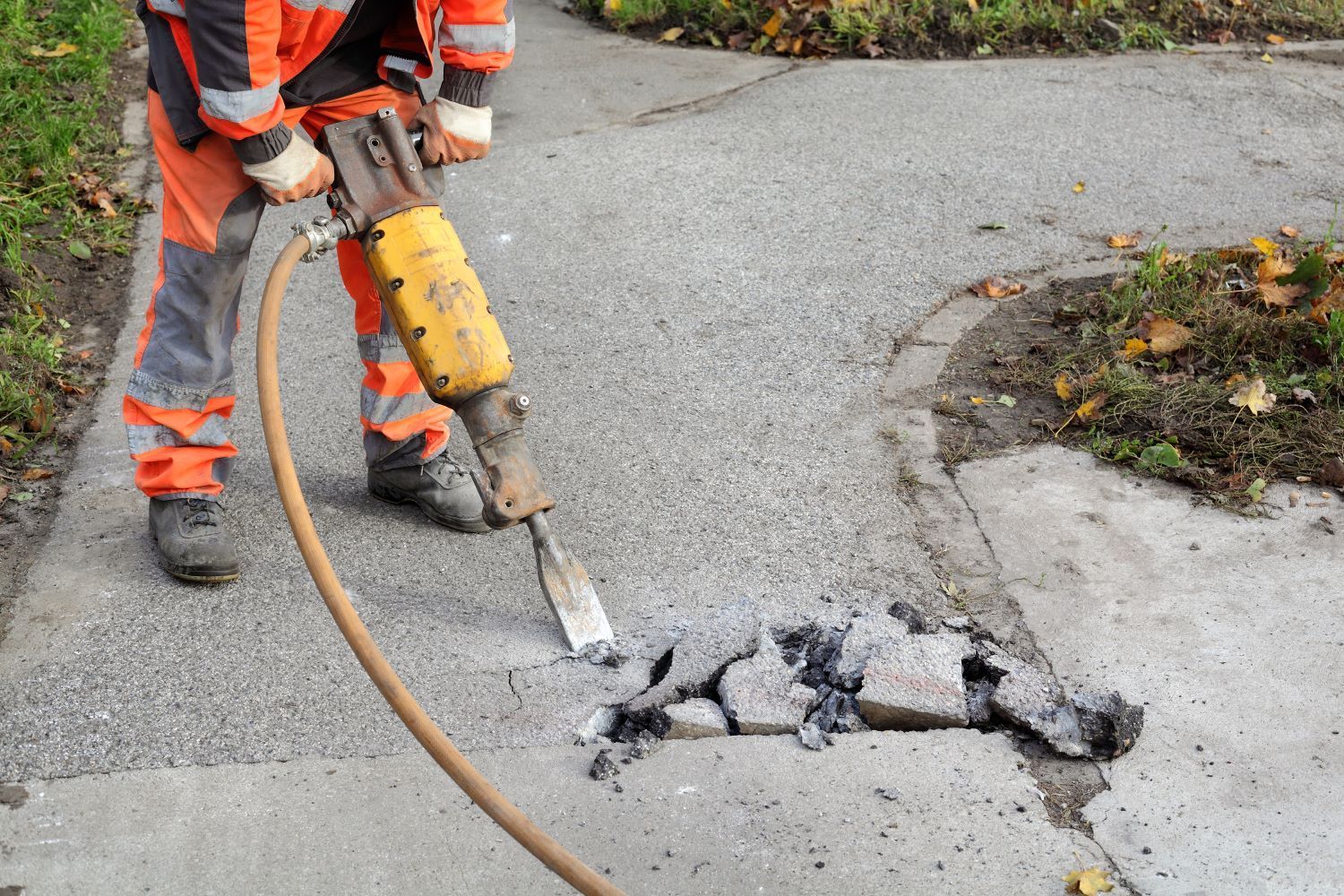
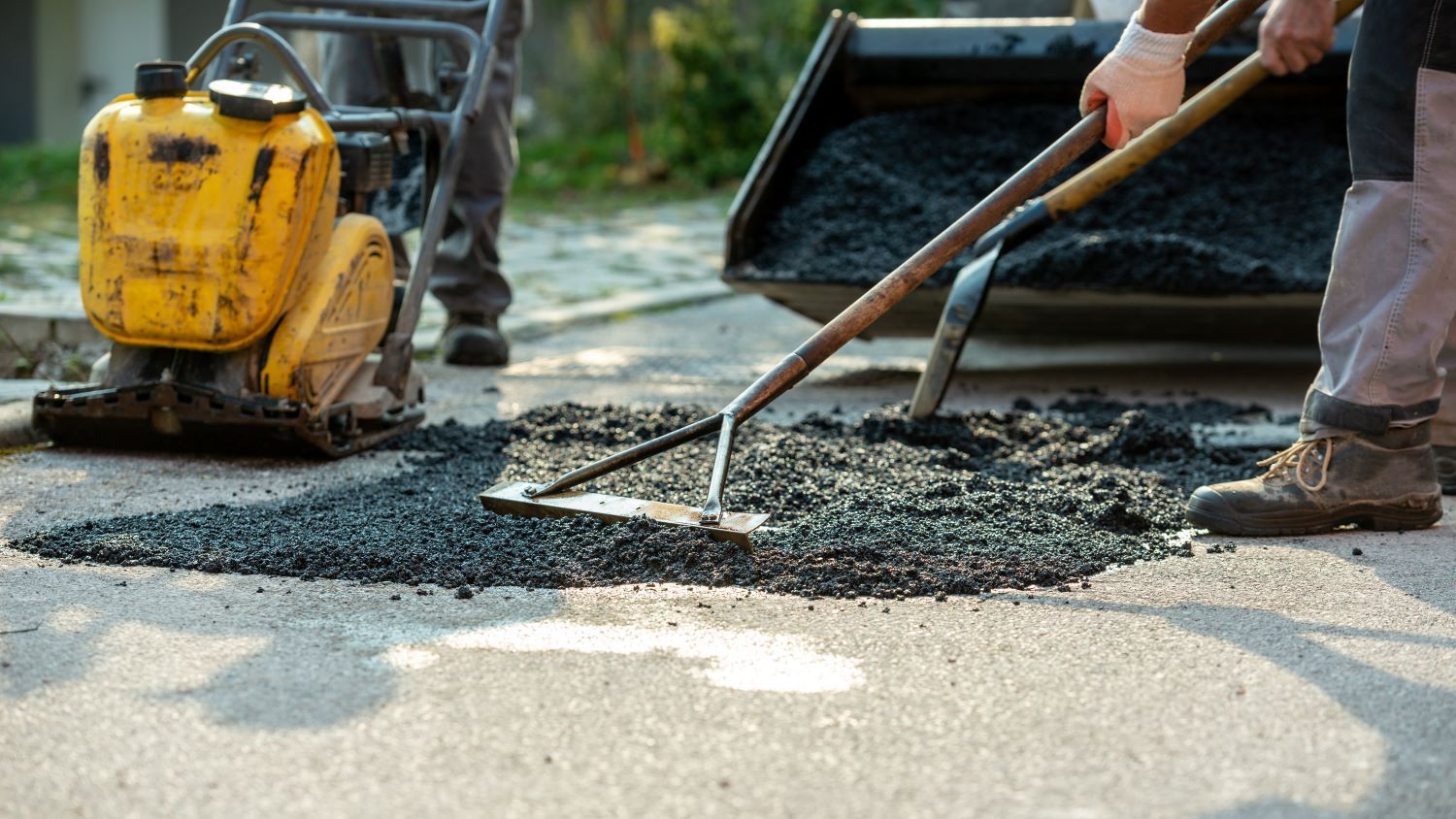
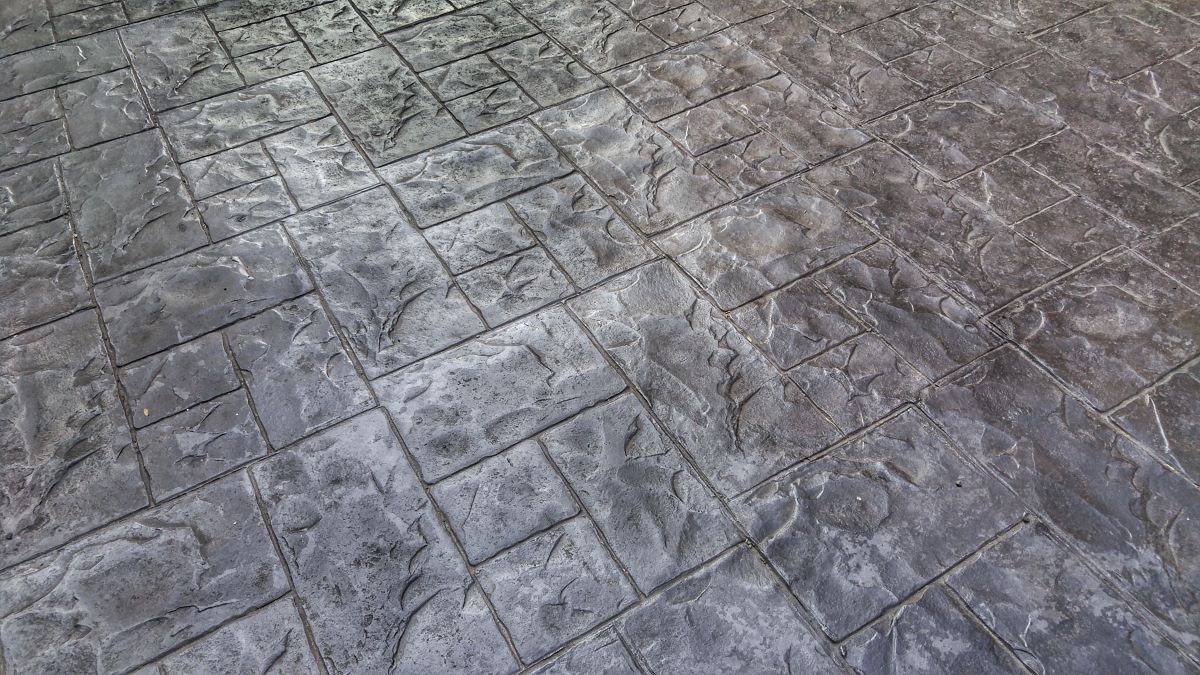
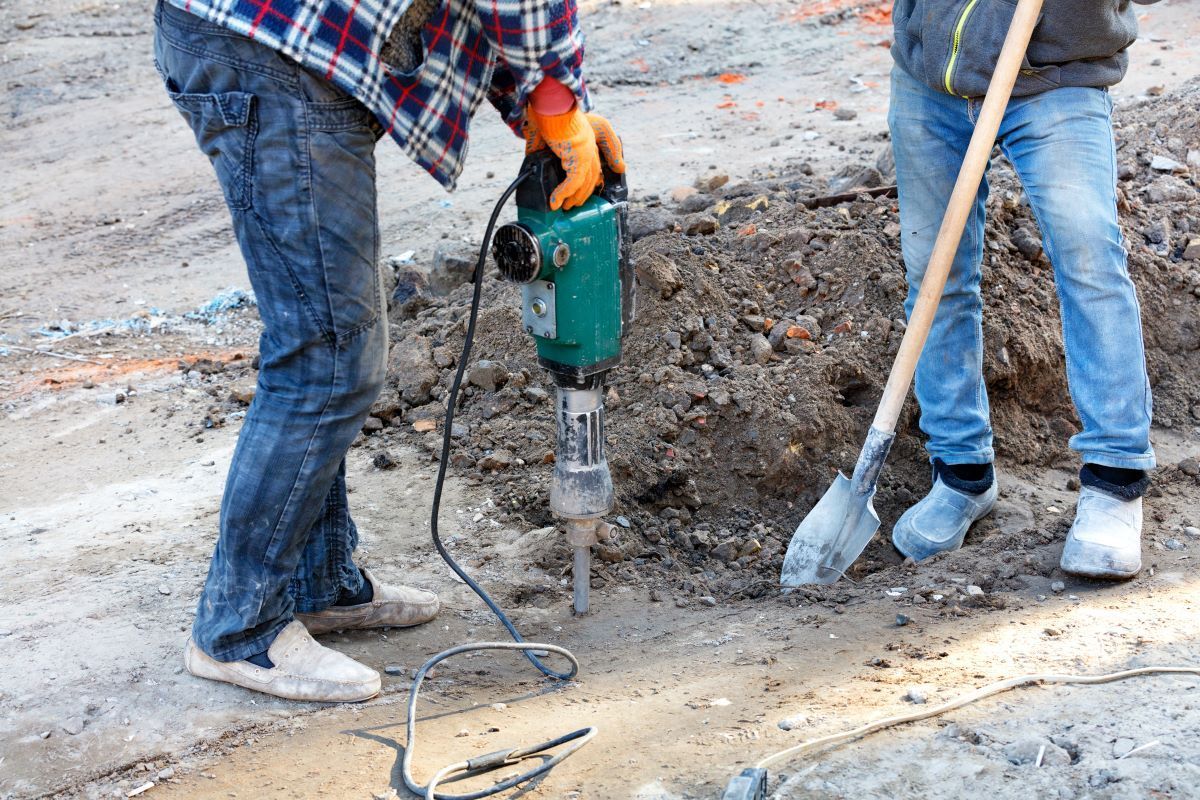
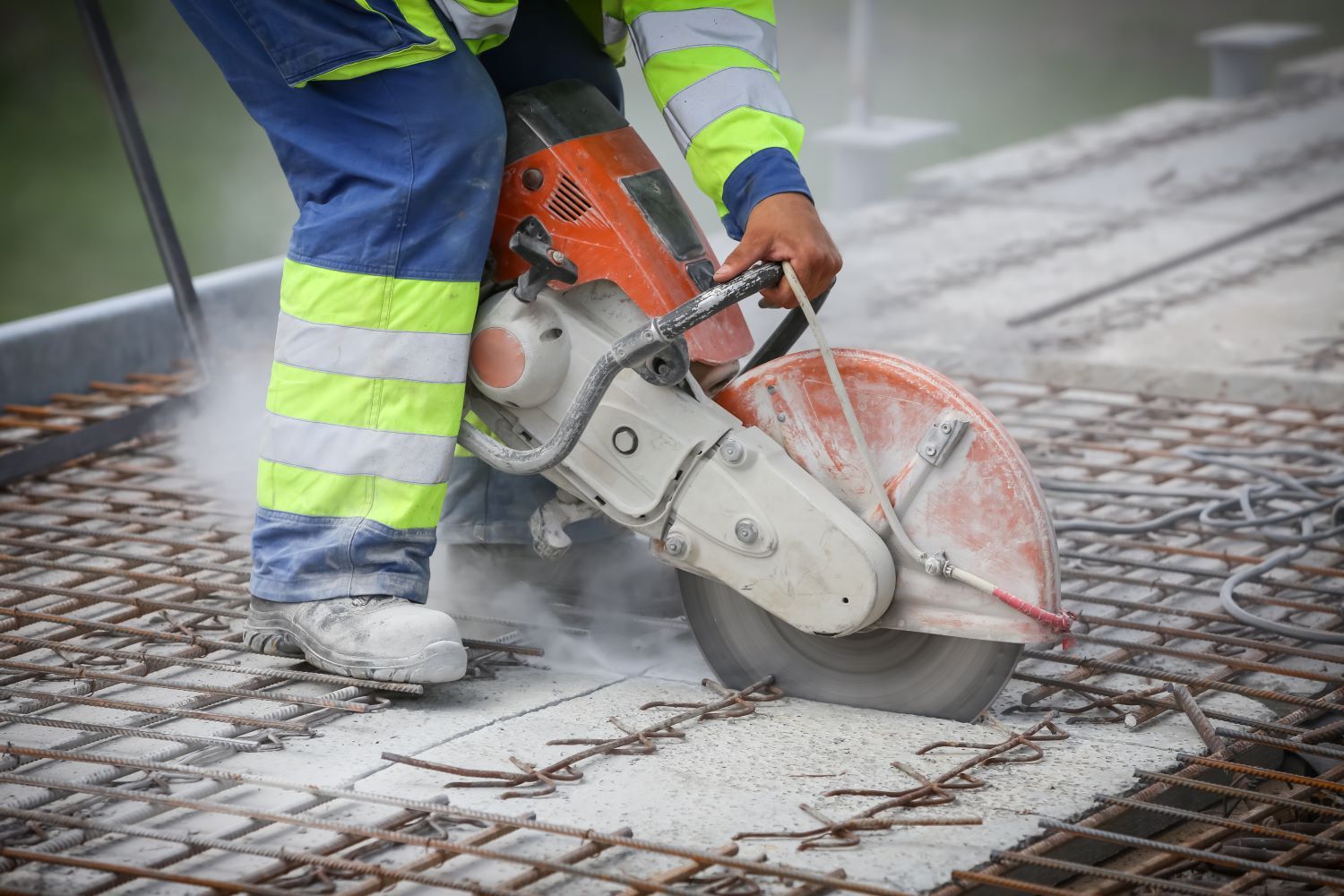
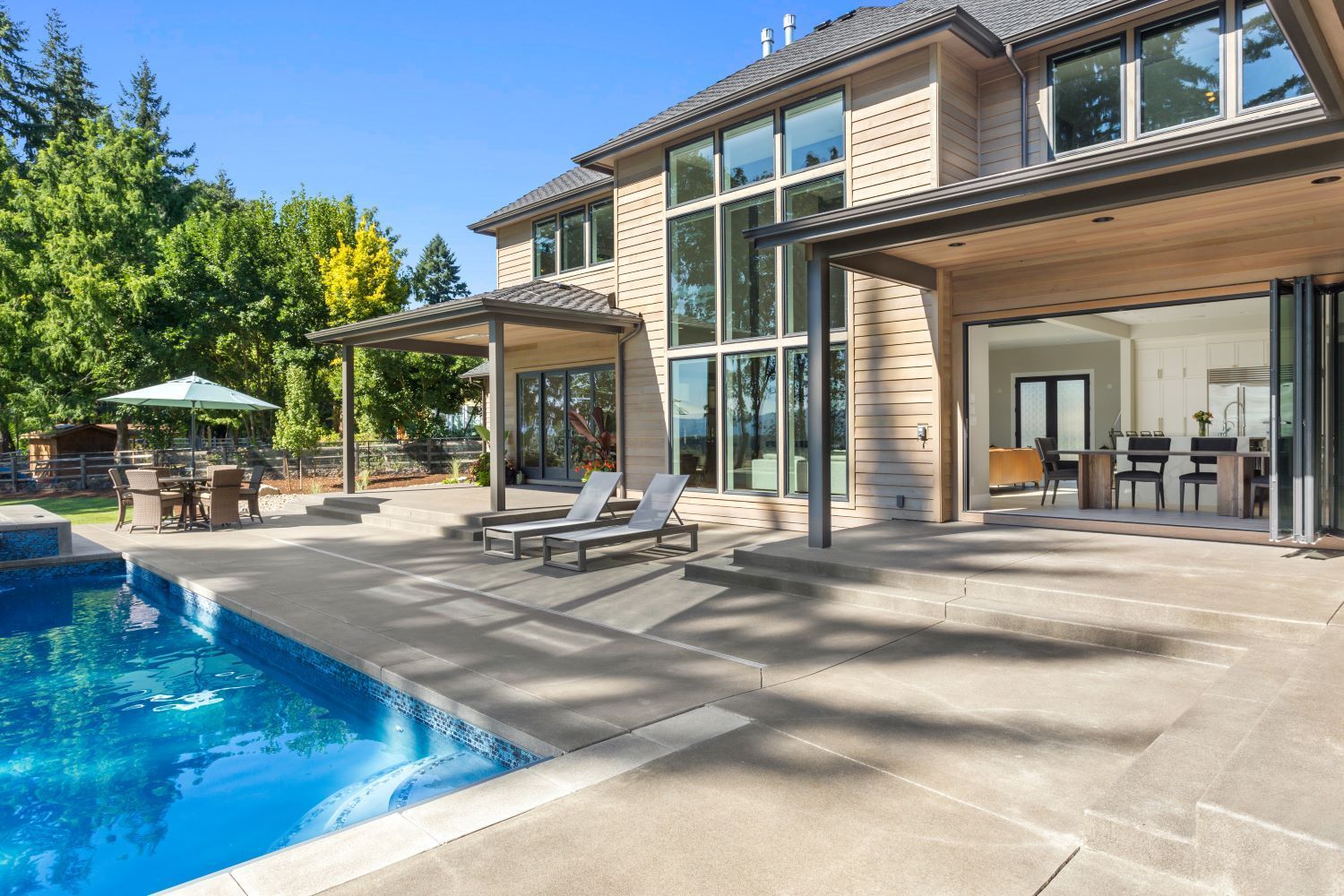
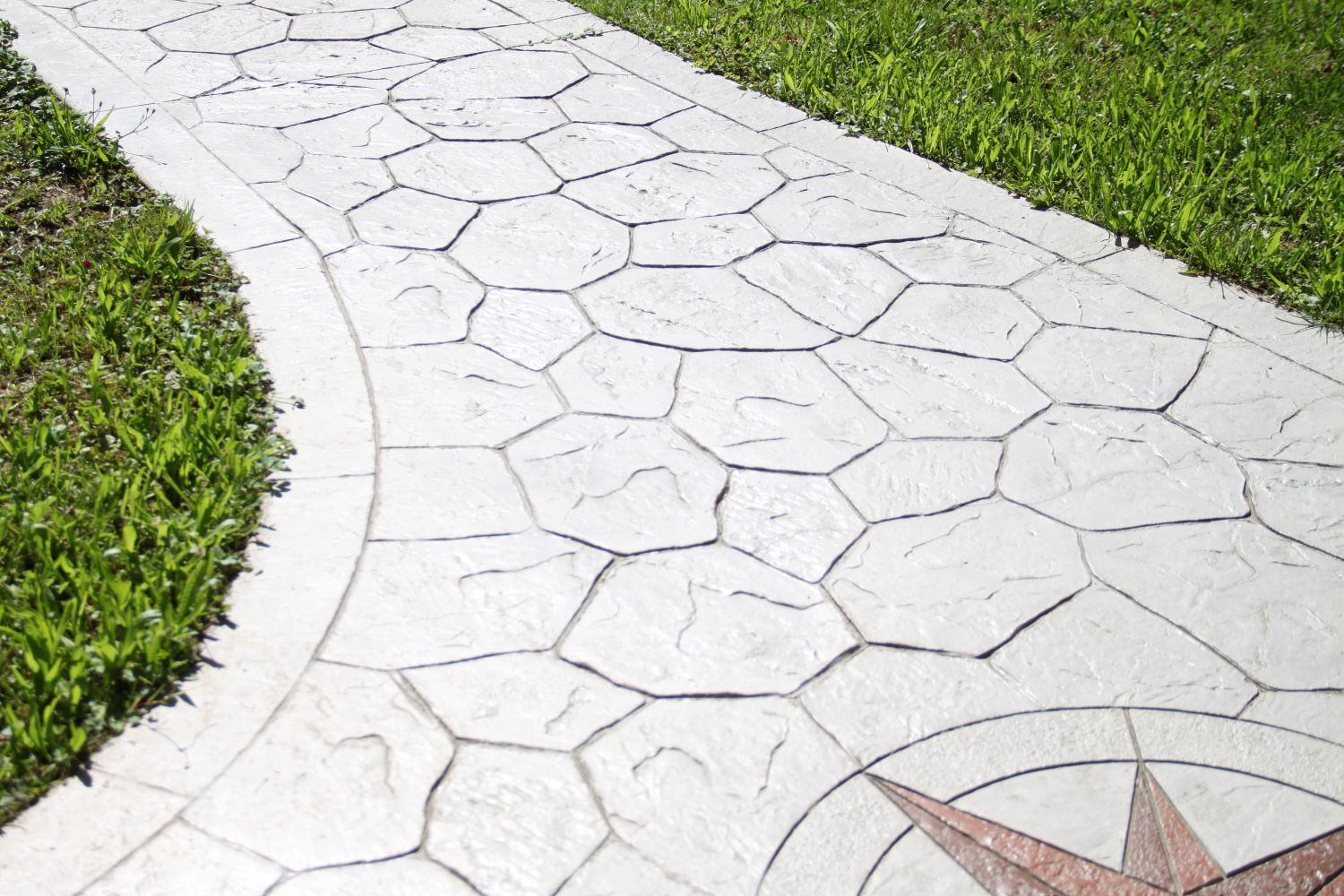
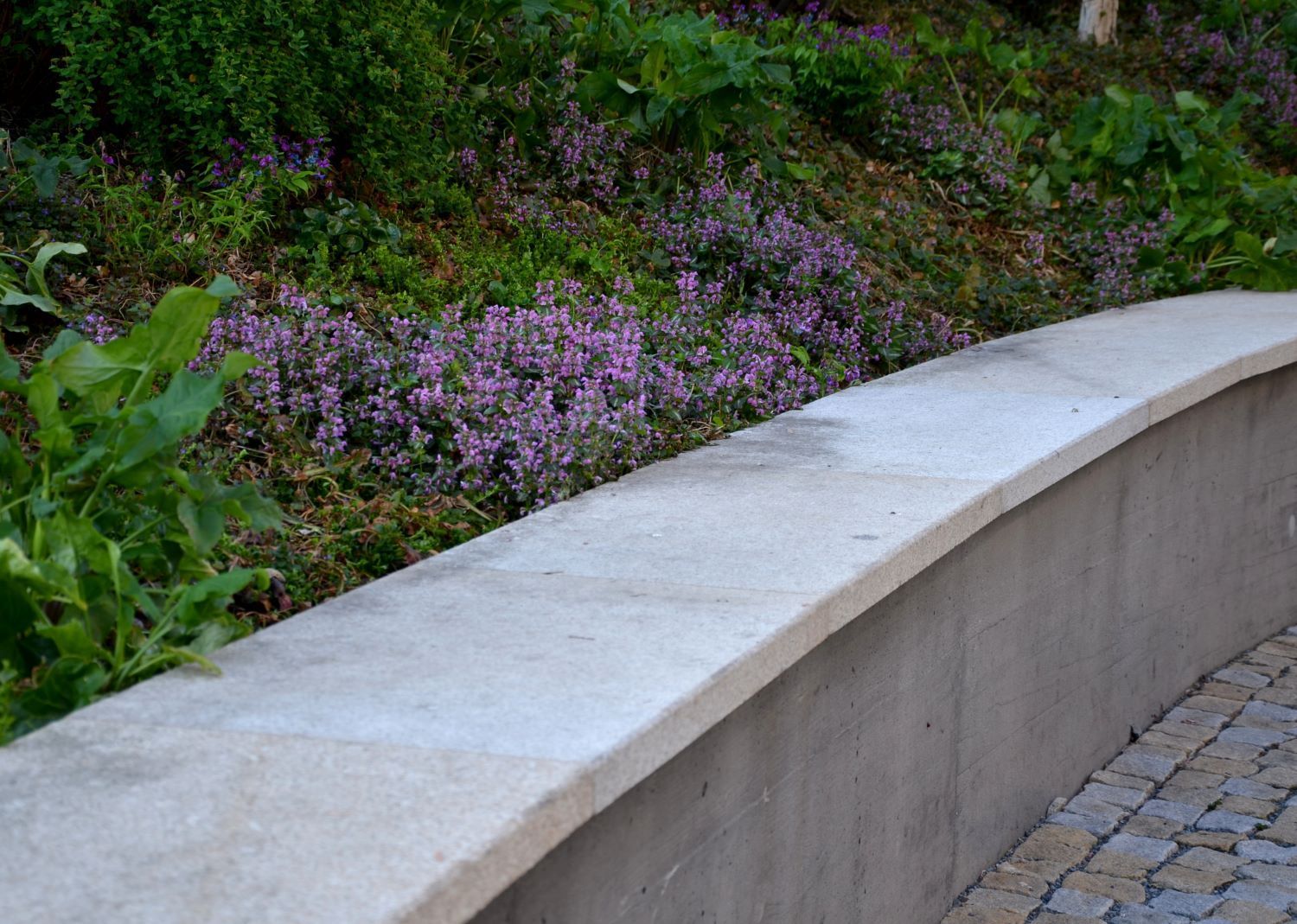
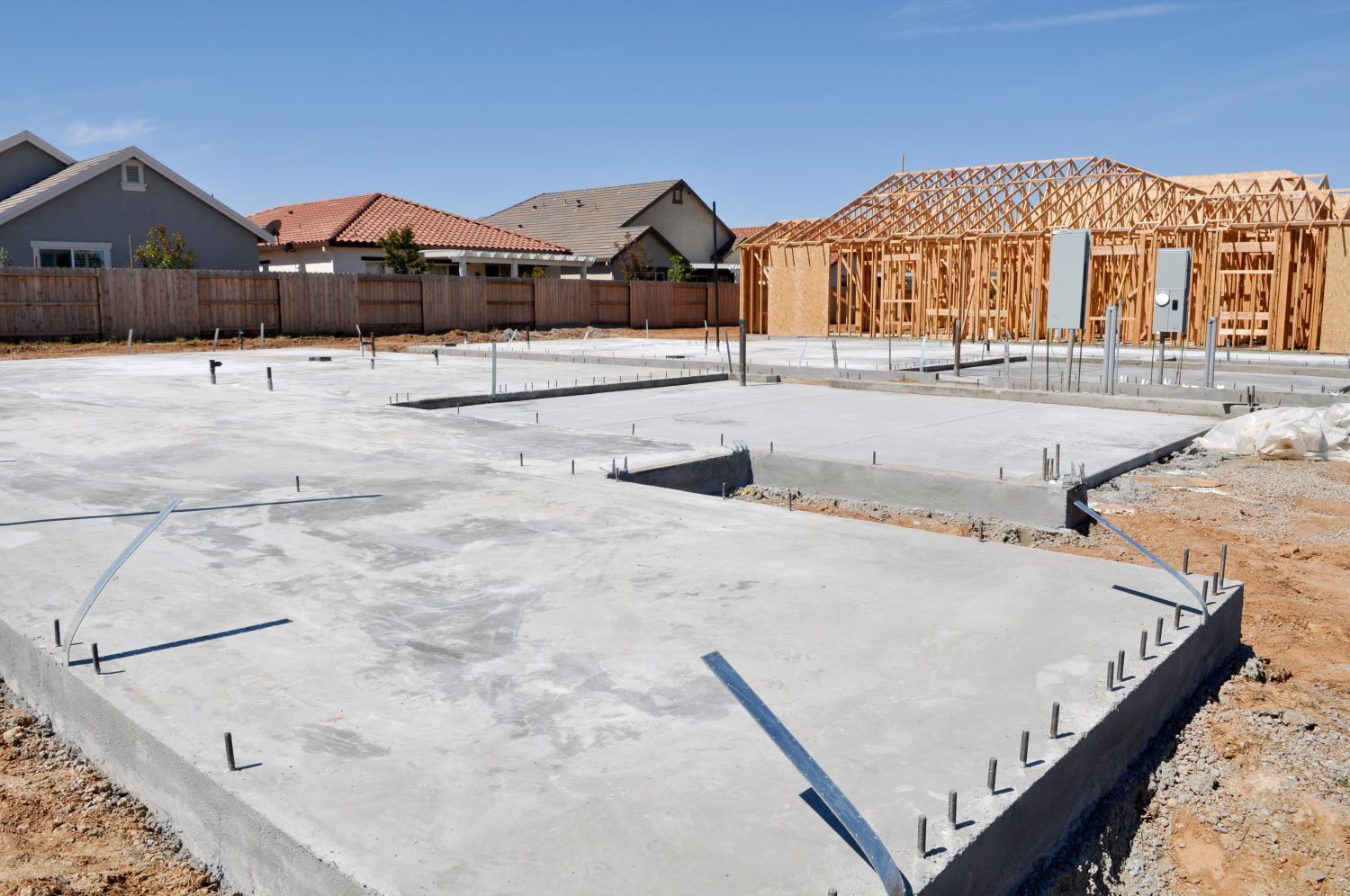